The History Of Traditional Canning
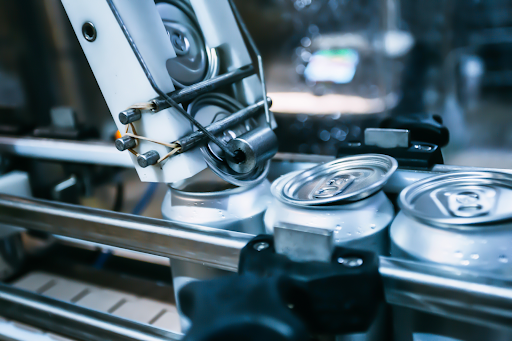
The year is 1795, with the infamous Napoleon seeking a way to preserve food for his vaunted army and navy forces. He offered a monetary reward of 12,000 Franks for whoever could devise such a solution, with the winner being Nicholas Appert in 1910 after he proposed sterilizing and storing food in hermetically sealed containers
Other important milestones in the history of canning beverages include:
The Limitations Of Aluminium Cans
Hard-to-hold beverages like kombucha or energy drinks can corrode the interior lining of cans, particularly if the liner application is inconsistent. Spray liners, for example, have micro-fissures that when combined with corrosive ingredients, become problematic.
Causes of Aluminum Can Corrosion
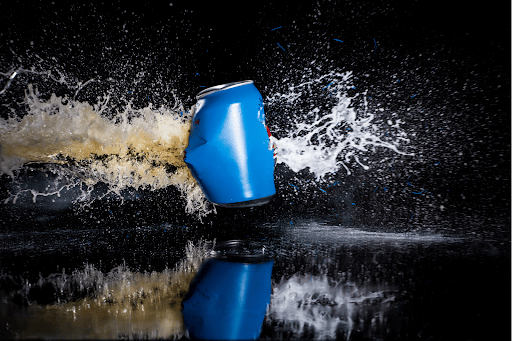
- High internal pressure or dissolved oxygen levels
- The liquid inside the can has a low pH
- The presence of chloride, copper, or sulphites
- High quantities of lactic, acetic, critic, and/or malic acid
- A drink having a high percentage of alcohol by volume (ABV)
- Inconsistent epoxy or BPA-NI can liner application
Types of Beverages That Require Specialized Cans

Kombucha
Kombucha, with its natural acidity and fermentation, can interact negatively with traditional aluminum cans. The acidic nature of the drink can compromise the liner of the can, potentially affecting flavor and safety. Canning kombucha with enhanced barrier protection is necessary to prevent these issues, ensuring the drink’s integrity and extending its shelf life without compromising taste or quality.
Coffee
Coffee, especially cold brew coffee, contains acids and oils that can react with traditional aluminum cans. Epoxy or BPA-ni can liner may not provide adequate protection against these compounds, leading to off-flavors. Canning coffee with advanced barrier properties is essential for maintaining the rich, smooth flavor of coffee while preventing contamination and preserving freshness over an extended period.
Energy Drinks
Energy drinks are often highly carbonated; they contain elevated levels of dissolved carbon dioxide creating intense pressure. They also frequently contain citric acids that corrode the interior lining, which can lead to adverse reactions when their vitamins, amino acids, and herbal extracts interact with the metal.
Cannabis-Infused Beverages
Cannabis-infused beverages face challenges with potency loss due to scalping, where cannabinoids adhere to the liner coating instead of being consumed. Traditional liners can exacerbate this issue, however, not all liners are made equal. Some are inert and prevent this adhesion, ensuring the cannabinoids remain in the beverage.
Cider
Cider’s natural carbonation and acidity levels, often contain sulphites, which can react with the raw aluminum can wall. This reaction produces sulphur dioxide, leading to potential off-flavors and quality degradation. Keep your cider crisp and fresh throughout its shelf life with specially designed hard-to-hold can coating materials.
Sports Drinks
Wine
Spirits
Liquor, such as whiskey, rum, and vodka, have high alcohol content, which can be particularly aggressive in compromising the efficacy of traditional can liners. Avoid aluminum can corrosion by opting for specialized cans with enhanced barrier protection to maintain the integrity and taste of spirits.
How Canning Technology Has Evolved
The most common thread across hard-to-hold beverages is the risk of their contents interacting with the can’s liner, thus exposing them to the metal. That’s why American Canning made it a point of focus with aTULC, the world’s first high-performance beverage can.
7 Steps To Assuring Quality Control When Canning Beverages
Inspect Raw Materials
It’s important to thoroughly inspect all raw materials—including aluminum sheets, liners, beverage ingredients, cans, lids, and packaging materials—to ensure they meet quality standards and are free from defects or contaminants. Regular testing for purity, consistency, and compliance with regulatory requirements helps maintain the integrity of the final product.
Sanitize All Equipment and Surfaces
Test Quality at Multiple Stages
- pH levels
- Sugar content
- Carbonation levels
- Microbial analysis
- Alcohol content
Compatibility Testing with Various Can Manufacturers
Regular Fill Level and Pressure Checks
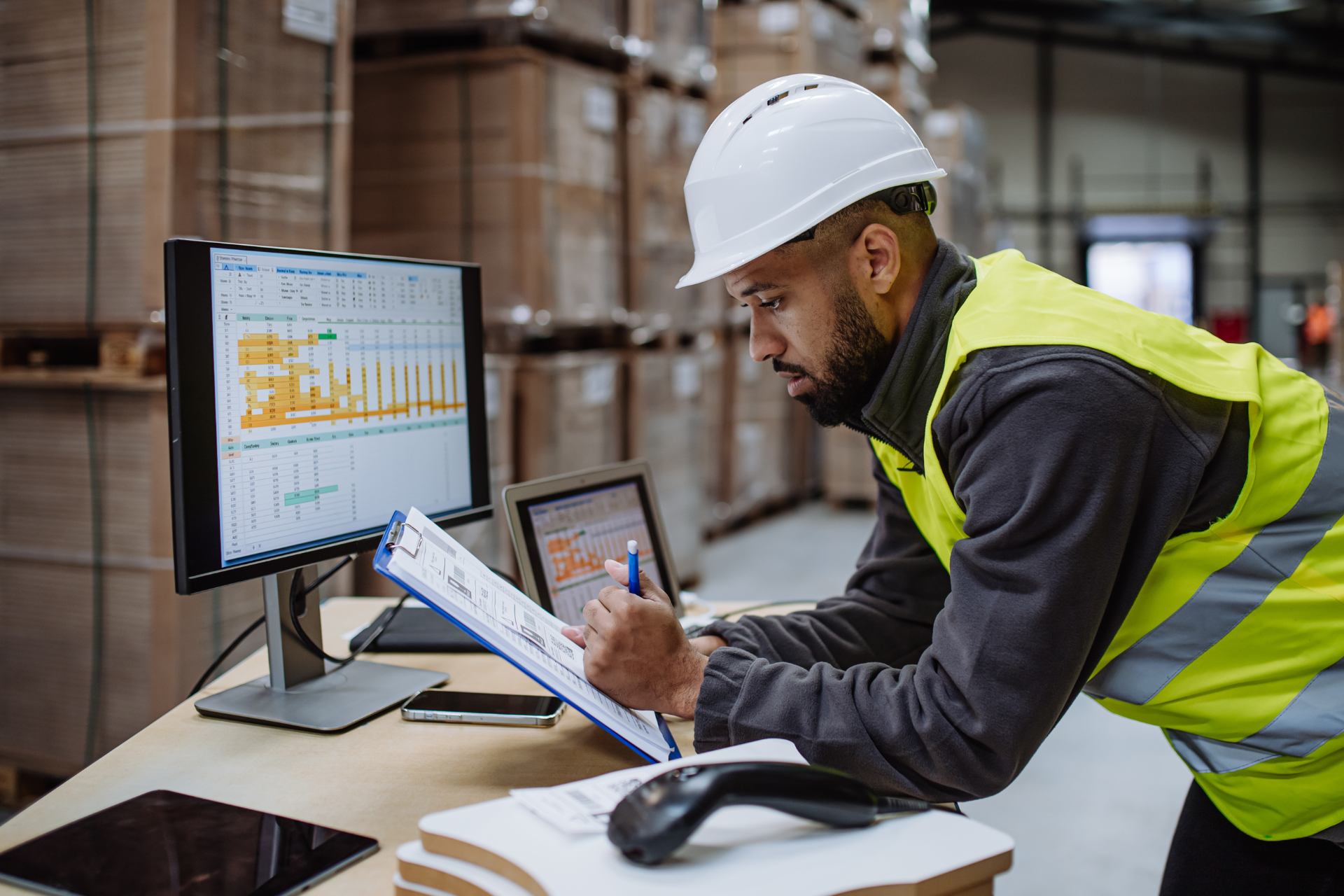
Monitoring Product Throughout the Supply Chain
Variables such as heat and prolonged storage at elevated temperatures can expedite reactions within the can, potentially affecting the beverage’s quality. By maintaining oversight throughout the supply chain, manufacturers can identify and address issues promptly.
Check Seal Integrity
How to Safely Ship Hard-to-Hold Drinks
Choosing the right canning material for your hard-to-hold drink and fine-tuning your processes is important, but so is ensuring they’re being shipped properly. All that careful consideration when canning beverages can be undone by an inexperienced or careless logistics team.
Partnering with a logistics team specializing in the beverage industry is the best way to ensure your product is handled with care. Third-party providers, like Brew Movers, understand the intricacies of each hard-to-hold beverage and will adjust their shipping and packaging processes and transportation methods accordingly to accommodate them.
Work with a team that provides temperature-controlled shipping solutions that further protect your beverages from heat and light exposure. Don’t underestimate the power of professionalism and experience when it comes to shipping hard-to-hold drinks!
Get More Out of Your Beverage Canning With Brew Movers
The science of canning beverages has come a long way, especially with aluminum can liner material. If navigating the complexities of hard-to-hold drinks is bogging down your operations, it may be time to streamline your supply chain with the team at Brew Movers!
Contact us today to learn how we can help you deliver excellence in every can.